2021年下半年,投资6亿元、占地80亩,年产500万台智能马桶坐便器的西马制造标准化基地已建成投用。在这个基地里,每30秒就有一台智能马桶完成组装 ,在通过多道质检关卡后,就能有序打包装车运往全国各地。
智能化生产车间集实验、生产、检测等功能于一体,全面导入MES+WMS生产信息管理系统,将智能制造工业5.0融入到高标准、高规格的流水线中,标志着西马正式迈向数字化高产业务。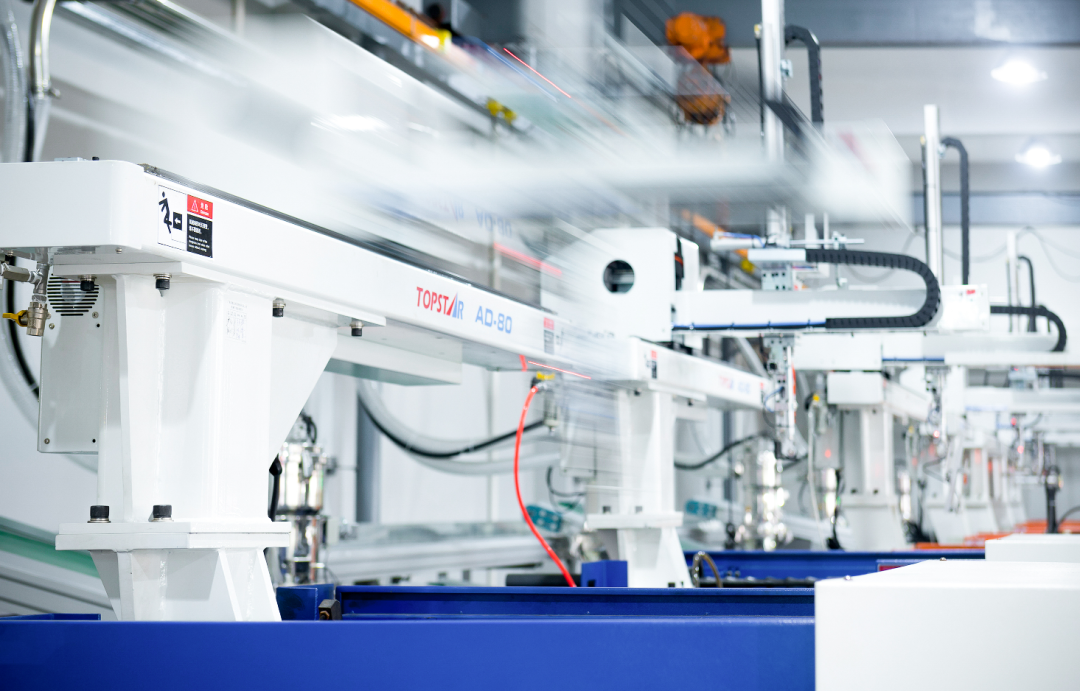
在制造端、产品端的主动变革,让西马树立起了堪称行业标杆式的“灯塔车间”。走进系统车间,1.5米长的MES数据监控屏幕上,计划达成、品质表现、生产进度等信息快速实时滚动。
这套斥资150万元打造的MES数字化系统,集成了从销售接单 — 下定指令 — 物料分配 — 车间生产 — 系统反馈等功能,让生产制造实现全流程信息化的高效闭环。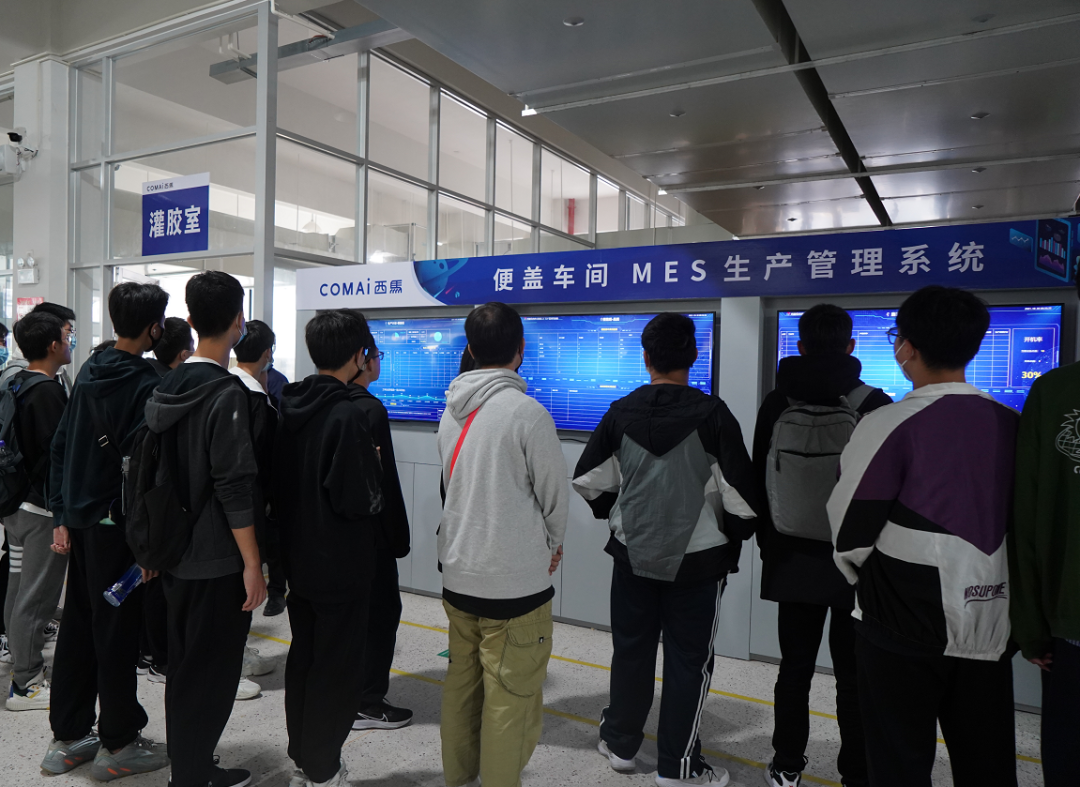
从接单到生产,以往信息流转至少要一两天,现在不到半天就能下单生产。在这条造价百万元的生产线上,有效缩减了人力成本。据统计,采用了数字化技术后,减少60%以上的设计修改与返工作业,生产工艺规划时间减少40%,产品上市时间缩短30%,制造成本下降15%左右。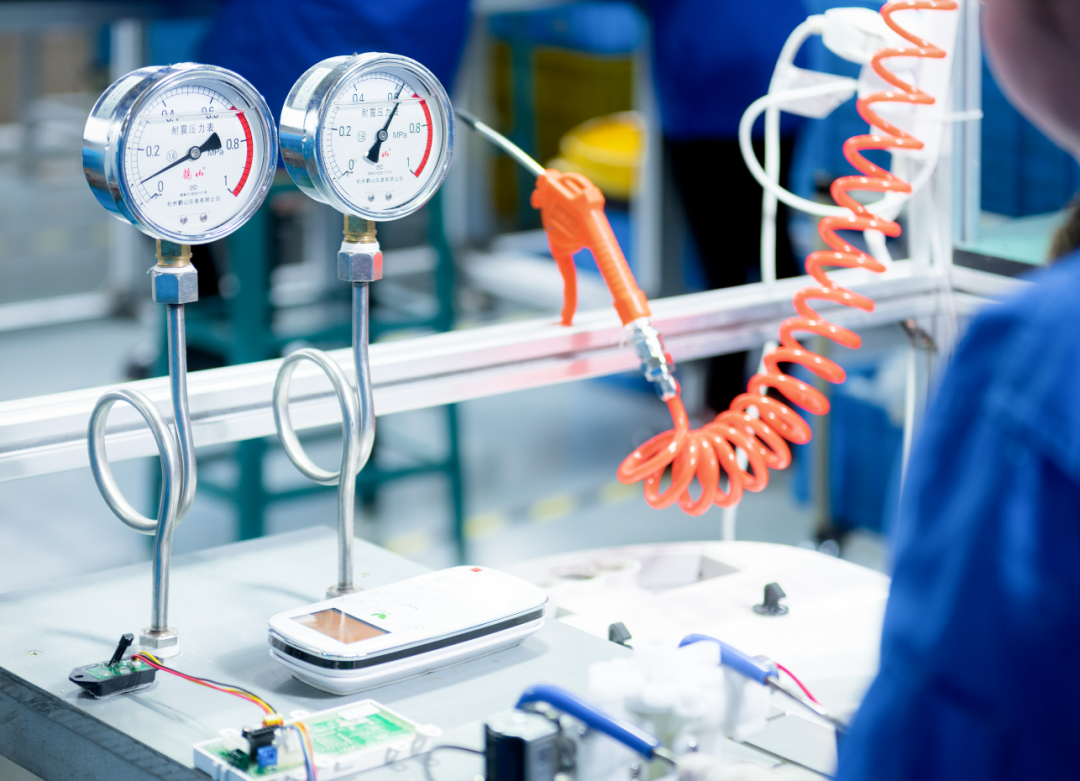
智能马桶难做,为何难做?良品率低,一直是制约行业发展的重要原因,其中的主要因素,就是产品后期检测不严格、不科学。西马斥资千万元配备高端实验设备,拥有CNAS国家级实验室,又花200多万元自主设计数字化检测系统,让每个便盖装配好后,至少要经过6道检验关卡。
在视觉防错工位,8个摄像头各司其职,从各个角度对准过检产品,确保检测全方位无死角。对产品来说,全程追溯能够解决产品批次的质量管理问题,能够缩小核查范围,从而节约人力物力成本。MES系统是实现这一切的关键。
这相当于产品的身份证,扫描包装上的二维码,马上就能看到产品在流水线上的每一个环节和责任人。“这样就确保生产责任到环节、到工人,实现物料全流程可追溯。”
“以往,产品虽然合格了,但在一些参数上仍有微小波动。”譬如,臀洗出水量上下波动50毫升,带给消费者的冲洗体验就完全不同。经过校验,现在每次出水量波动控制在10到20毫升,这样就确保了在节水性和体验感上达到平衡。“经过一系列的调整和检测,光是便盖出厂前就至少要经过65000次翻盖。以一个家庭每天使用10次计算,我们的产品至少可以用10年以上。
卫浴行业基本上仍属于劳动密集型产业范畴,如何从劳动密集型向技术密集型转变?这是西马一直思考的问题。目前,西马每年研发投入都在千万元以上,在行业中属于领先水平。在西马智能化车间里,每30秒就有一台智能马桶完成整机组装下线,这样的生产效率比行业平均水平提升了整整1倍,而其出厂质量一次性合格率更是达到99%以上。“未来这里将是国内最先进智能马桶制造基地,是智能马桶检测、实验中心,是智能马桶的绿色工厂,也为我们在大健康、新技术、互联网、物联网等实现重大突破打造平台。在打造千亿级智能家居产业布局当中,西马希望可以起到领头羊的作用!COMAi西马已搬至新研发基地,欢迎喜欢西马和智能生活的伙伴们前来参观
声明 :以上部分图片来源于网上截图,如需更改,请联系西马公众号进行删除